Rebuild Process
Twenty Years in the Making
Our rebuild process has been refined over 20 years. Each one has taught us something new about our seamers and how to get them running at optimal performance.
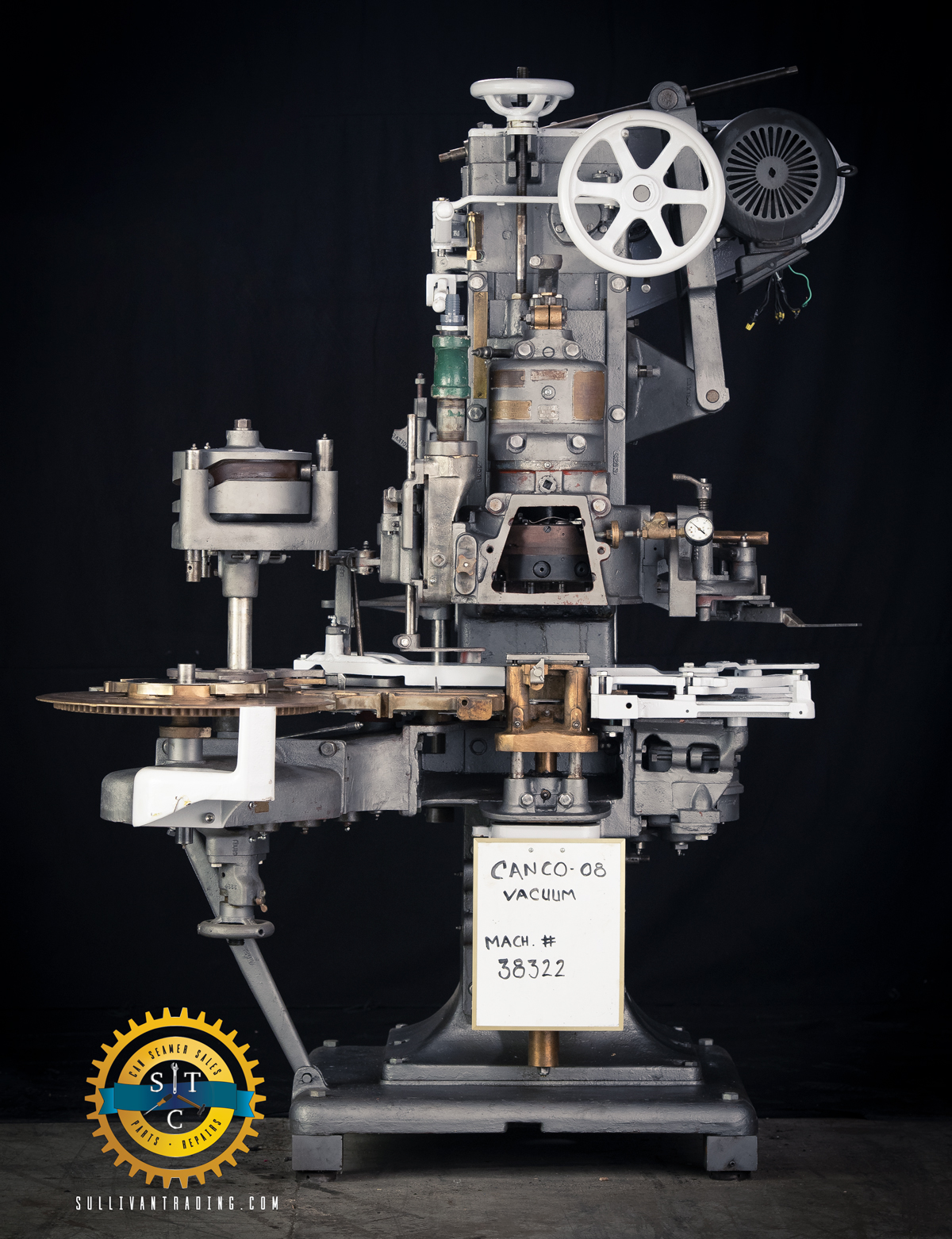
Around the shop we call our rebuilds "the gold standard" because they are born out of love.
Our appreciation for Canco seamers came about the old fashioned way - by tearing them apart and putting them back together.
Before we rebuilt them we ran them in a coffee line. That experience provides us with first hand knowledge in the food packing industry..
Over the course of hundreds of rebuilds we developed a standard that takes into consideration the most likely points of failure and reflects a "quality in - quality out" philosophy.
Tear Down
As each of the the working parts is removed from the machine they are examined for excessive wear.
Parts Cleaning & Inspection
We run the hardest working parts through an ultrasonic cleaner to remove grease and grime. Then they are wire brushed and inspected for any excessive signs of wear and damage.
Housing Strip Down
The machines we pull out of service have been worked hard. So we strip down them down to bare metal and remove old grease and paint flakes in the process. This gives us a clean metal housing which we coat in Steel-it Alkyd Primer to prevent rust.
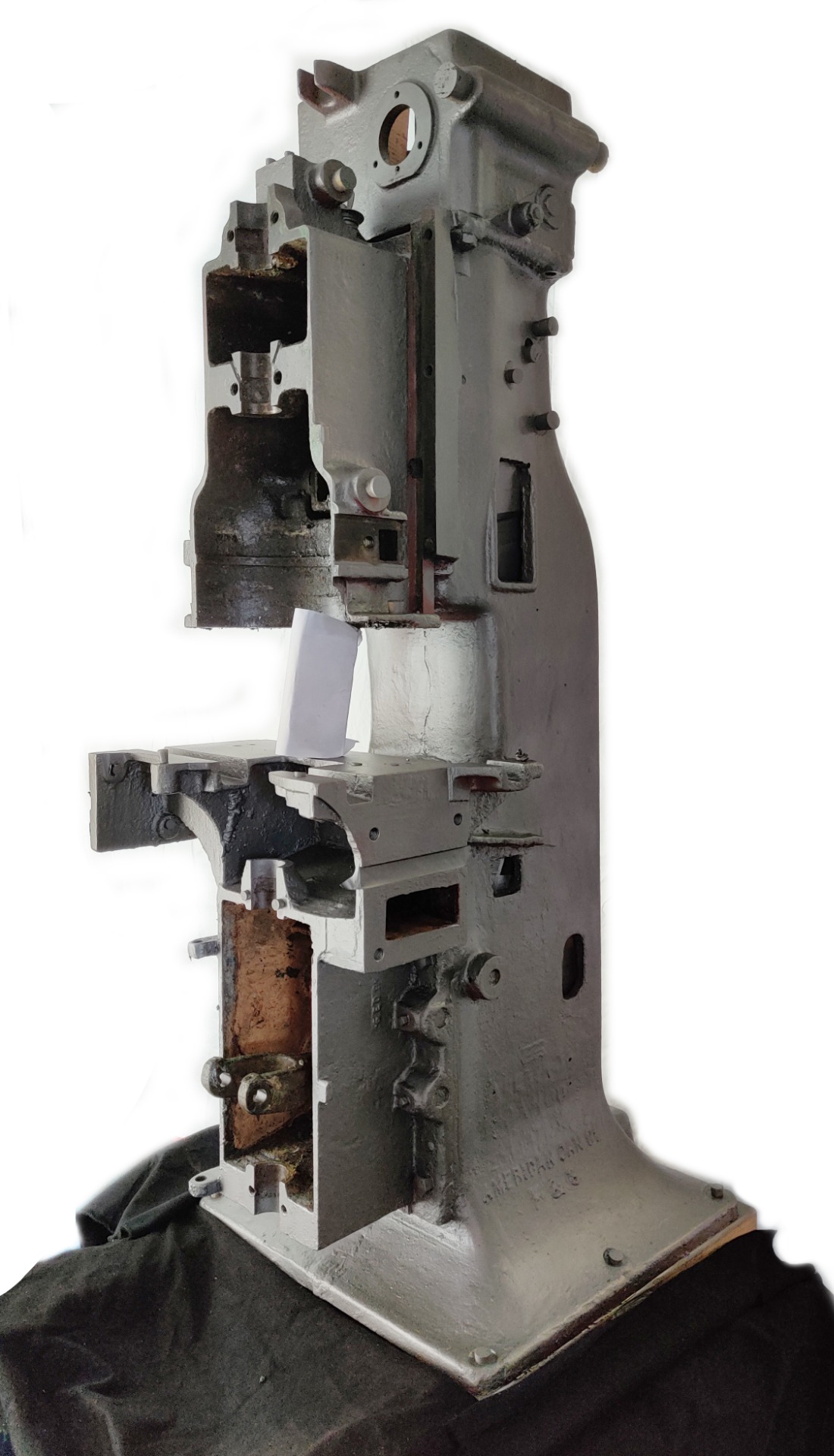
Housing Prep & Paint
Before paint we take care to avoid overspray in the the cam shaft opening or any bolt holes. Our paint of choice is Steel-it Stainless Steel Polyurethane. It provides a long lasting finish that is FDA-approved.
Parts Replacement
Parts showing excessive wear are replaced from our inventory.
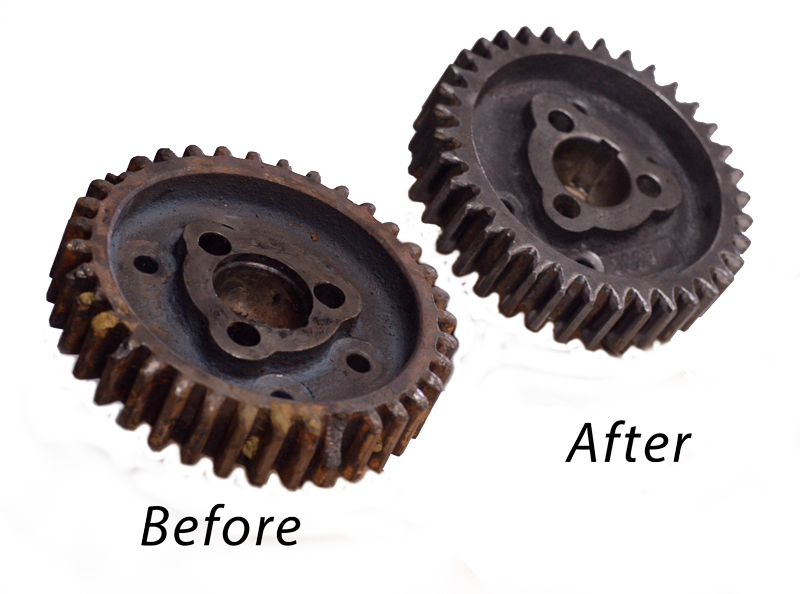
Example of a drive clutch gear replaced after inspection
Hardware Upgrade
We remove rusty bolts and replace them with new stainless steel fasteners making them resistant to corrosion as well as easing all future maintenance.
Paint and Powder Coat
A selection of parts are sent out to be professionally sand blasted and powder coated such as the hatches, handles, and can contact parts. This makes sure they stay sharp and presentable for years to come. Our powder coat paint is FDA-approved coating.
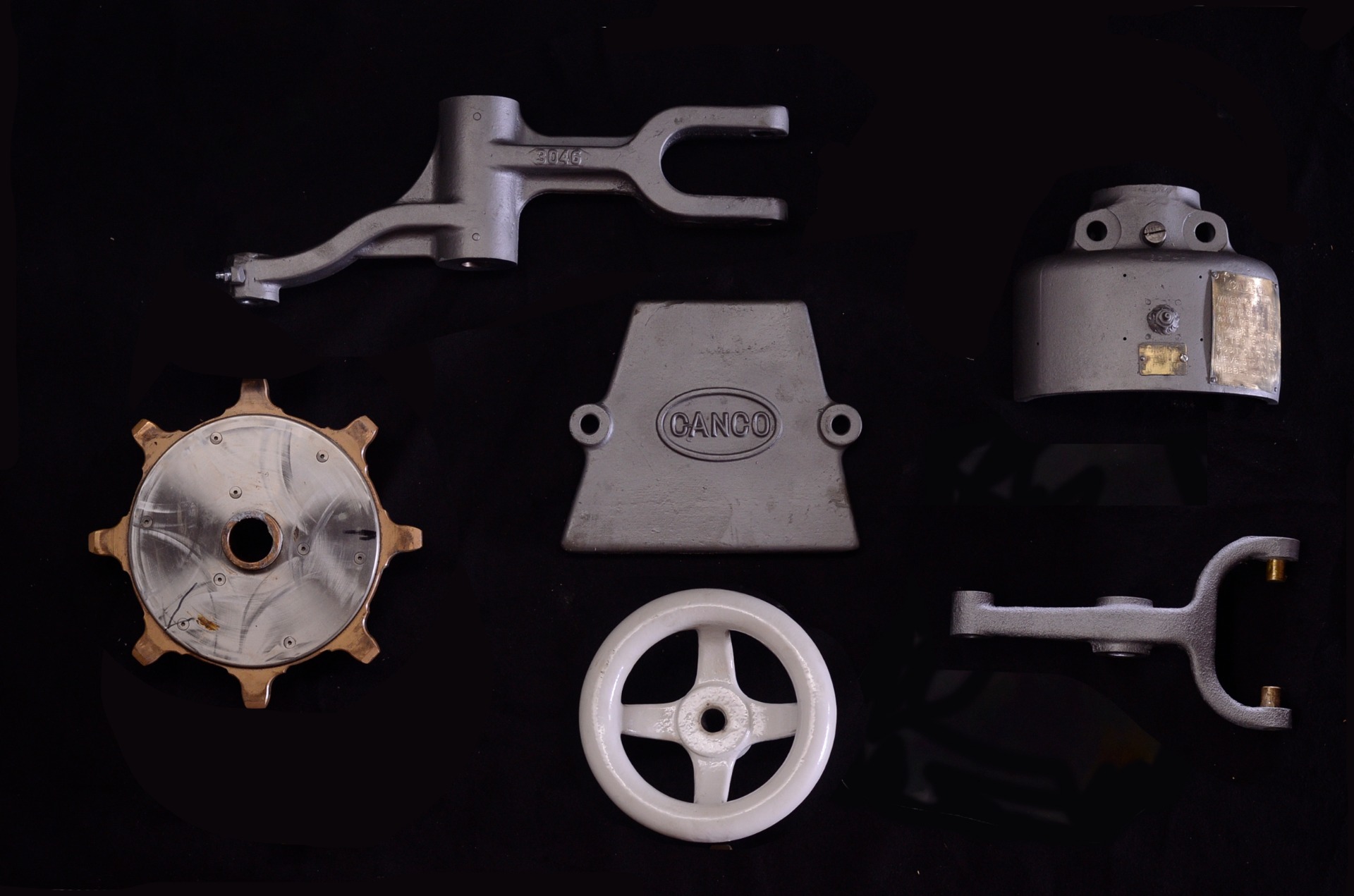
New Motor
Our rebuilds get a brand new motor which is setup for 3-phase 230V or 460V depending on our clients needs.
Fit Up
The machine parts are installed back in the machine. Each piece is appropriately oiled and greased to allow for smooth operation.
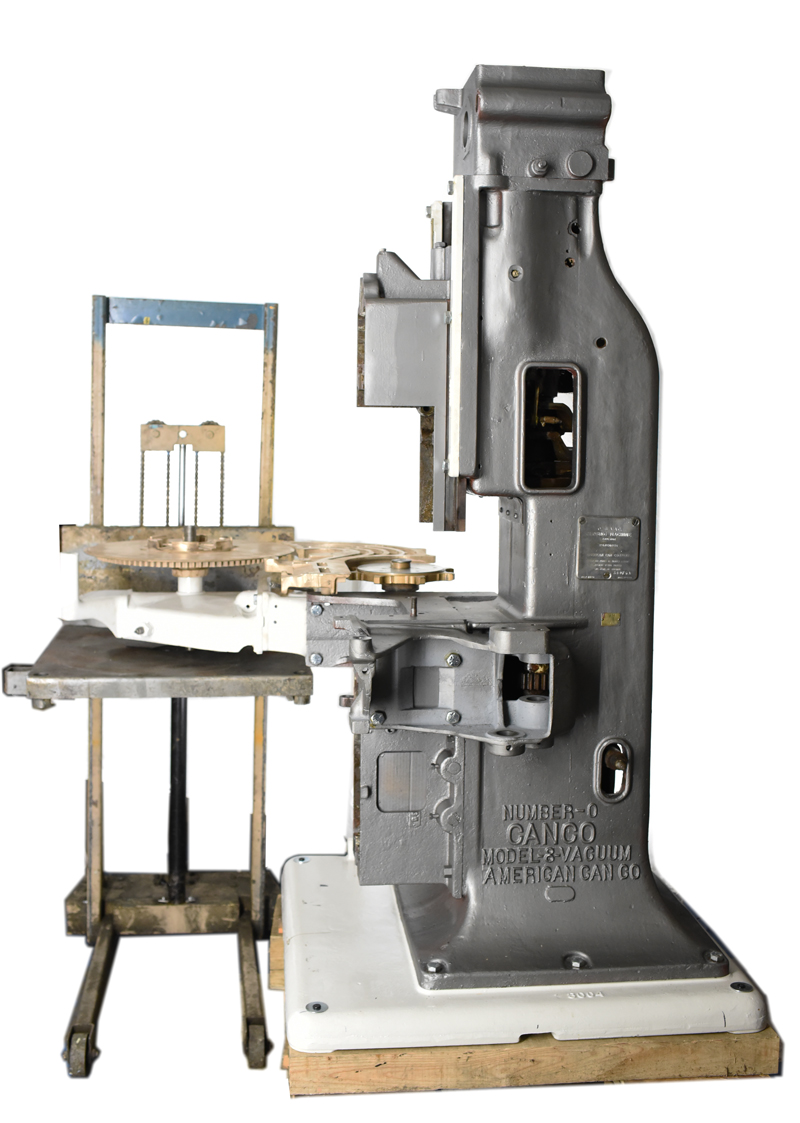
Seaming Height Adjustments
We set the seaming height according to our clients request. Final adjustments should always be made on site.
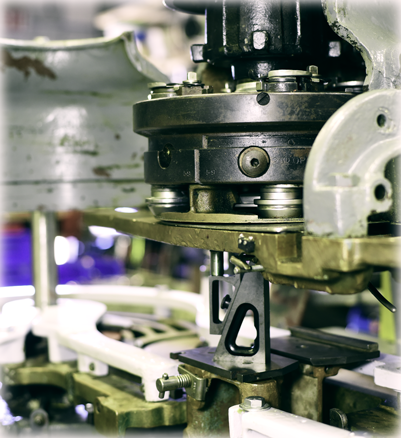
Testing
We run 100-200 customer supplied of cans and ends through the machine to make sure timing and can handling is correct. Can seams are set to customer supplied specifications. It is clients or can suppliers responsibility to perform final adjustments on site to their in-house quality control standards.
Shipment
We land the machine on a sturdy pallet and bolt it down for a smooth trip to our clients. Full crating is available for international shipping and special order.
Interested in a rebuild?
For faster service utilize our Build a Quote page